Innovative materials help NEV power batteries stay away from fire hazards
In recent years, the electrification of automobiles has become a major global trend, with the demand for new energy vehicles (NEVs) growing in many major automotive markets. However, the risk of thermal runaway in high-voltage lithium-ion batteries, causing electric vehicles to catch fire or even explode, has always been a serious concern for consumers, battery manufacturers, and automotive OEMs.
Although early published evidence suggests NEVs are less likely to catch fire than internal combustion-powered vehicles, the known flammability of lithium-ion cells and the media attention point towards the application of innovative flame-retardant materials as one of the keys to addressing the safety issue of NEV power batteries.
The Flame-Retardant Mechanism
To effectively address the fire hazards of NEV traction batteries, it is necessary to understand how flame retardants slow the propagation and assist in the extinguishing of fires. The occurrence of combustion usually requires three major components; the object that acts as the fuel to be combusted, the addition of heat, and a combustion aid – oxygen is an example of a naturally occurring aid. Usually, a lithium-ion battery fire is caused by a short circuit associated with over-charging or discharging or internal mechanical damage to the cells. Many higher energy-density lithium-ion chemistries are sensitive to raised temperatures, and once combustion starts, they create more heat and oxygen, which propagates the fire, risking neighbouring cells.
Functional layers and barriers are used in the battery pack to protect neighbouring cells from the heat and flames of a decomposing cell. There are also other materials in the pack, that improve the packaging, assembly, and performance but are not inherently heat or flame-resistant. These often polymeric materials may need to contribute to slower fire propagation. The judicious application of heat-resistant and flame-retardant materials will help in this regard, thus avoiding the thermal runaway phenomenon and reducing the risk to lives and property.
"The easiest way to make a material flame-retardant is to add flame retardants. Taking common phosphorus-based flame retardants as an example, when combustion occurs, they decompose under high temperatures to generate phosphoric acid. "
Reacting to high temperatures on the polymer surface, phosphoric acid dehydrates the polymer quickly to form a carbon layer, which can effectively block the contact between oxygen and the polymer, while cutting off the transfer of heat to the polymer. The flame-retardant effect is achieved through both oxygen starvation and heat insulation.
In addition to phosphoric acid, phosphorus-containing flame retardants will also generate a large amount of phosphorus-containing free radicals. These can effectively extinguish the combustion-supporting carbon- and oxygen-containing free radicals in the air, thereby contributing to the flame-retardant effect.
Test Standard for Flame-Retardant Properties
But how can the industry evaluate the flame-retardant properties of a material? A common test method is taken from the UL 94 standard describing the burning behaviour of plastic materials. Originally written to set safety standards for plastic materials used in devices and appliances, it has been adopted by many in the NEV industry. One of the popular test methods involves a specimen being made into a thin shape of a specified size and clamped in the specimen holder before it is burnt vertically with a flame.
This test works where the specimen does not retract from the flame, but it has its limitations when evaluating the flame-retardant properties of a thin material such as a pressure-sensitive adhesive or film. The UL 94 test standard includes a method for such thin materials, where the behaviour is rated under five criteria and the best performing given a VTM-0 classification.
The UL 94 V type test should then be performed with the thin adhesive tape or film applied to the intended substrate to replicate the actual application and prevent materials from distorting and moving away from the applied flame.
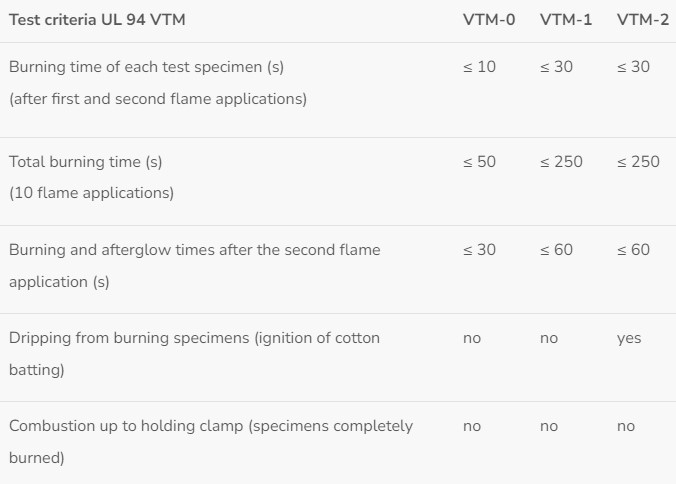
Avery Dennison’s Flame Retardant Technology Platform
As one of the leading suppliers of pressure-sensitive adhesive solutions, Avery Dennison has been working with flame-retardant materials for years. Today, it owns an advanced technology platform and extensive solutions. Avery Dennison can provide comprehensive solutions to meet customers’ different needs.
The first solution is that the adhesive itself does not have flame-retardant properties, but when applied to a flame-retardant facestock, the solution offers flame-retardant properties conforming to the UL 94 VTM-2 classification. The second solution is where the adhesive is mixed with a flame retardant and after physical mixing, delivers flame-retardant properties compliant with the UL 94 VTM-0 classification.
The premium solution builds on Avery Dennison’s specially designed polymer, the main chain of which contains chemical substances with flame-retardant properties, thereby making the polymer flame-retardant. Only a small amount of external flame retardant needs to be added to the polymer in the adhesive to meet the UL 94 VTM-0 classification standard – the solution is usually suitable for products with ultra-thin structure or very high shear strength.
Flame Retardant Adhesive Technology
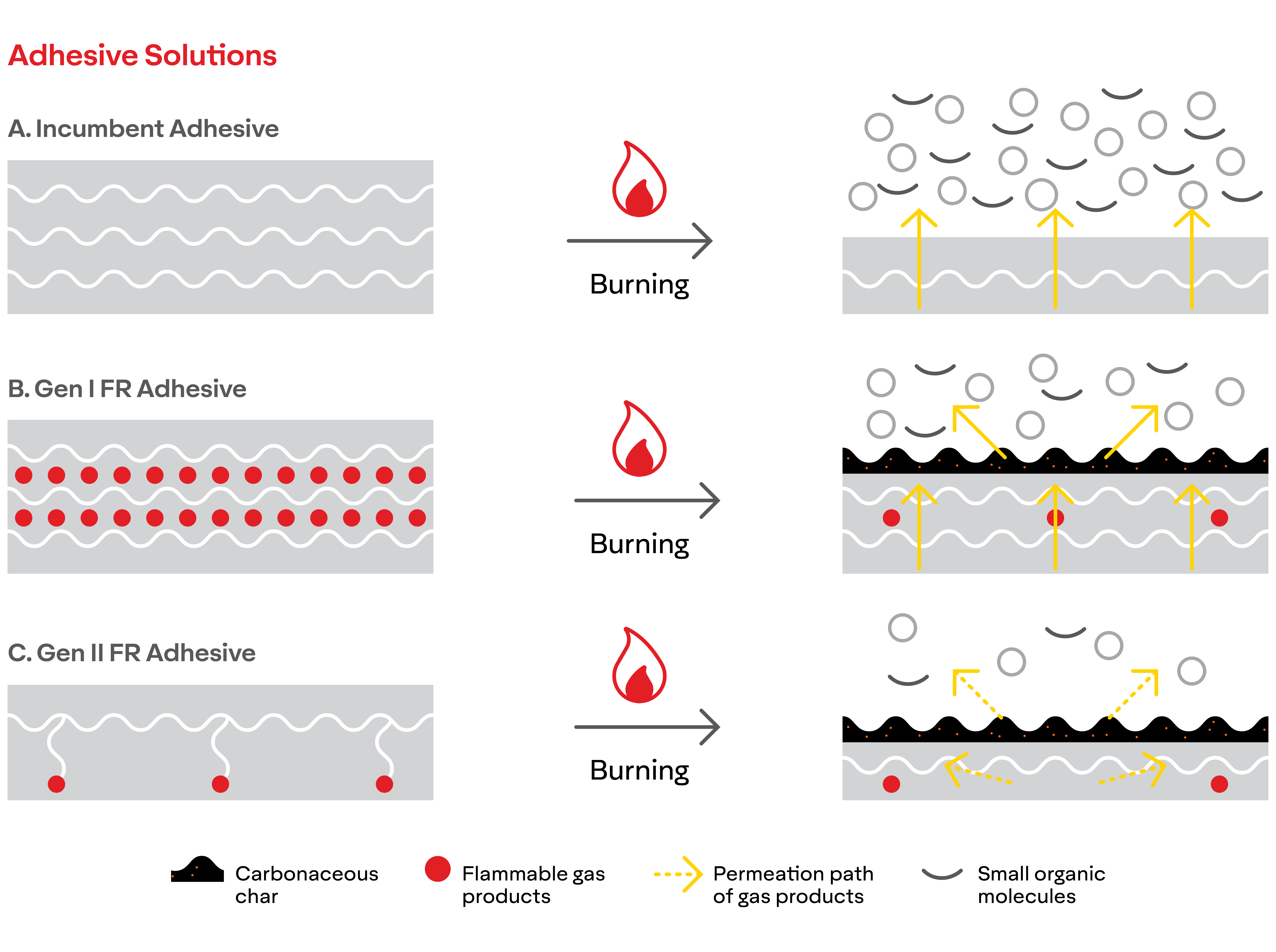
Adhesive Solutions
A. Incumbent Adhesive
- Non FR adhesive
- With FR face stock to achieve UL© VTM-2
B. Gen I FR Adhesive
- UL VTM-0
- Solvent adhesive physically blended with FR additives
- For general portfolios
B. Gen II FR Adhesive
- UL VTM-0
- Adhesive chemically crafted with FR compounds
- For thinner and high performance portfolios
In addition to its adhesive technology platform, Avery Dennison also boasts comprehensive coating solutions that deliver many different functionalities and customer benefits. Through the physical addition of flame-retardant coatings on polymer films, the conventional adhesive coating solution can also offer flame-retardant properties, meeting the UL 94 VTM-0 classification.
The technology highlight of Avery Dennison’s premium flame-retardant coating solutions is a specially designed telechelic polymer. This captures and holds the flame-retardant additive tightly, enabling the material to deliver outstanding flame-retardant properties while giving the coating layer better transparency. The application of this technology can also effectively prevent combustibles from dripping during flammability testing.
Flame Retardant Coating Technology
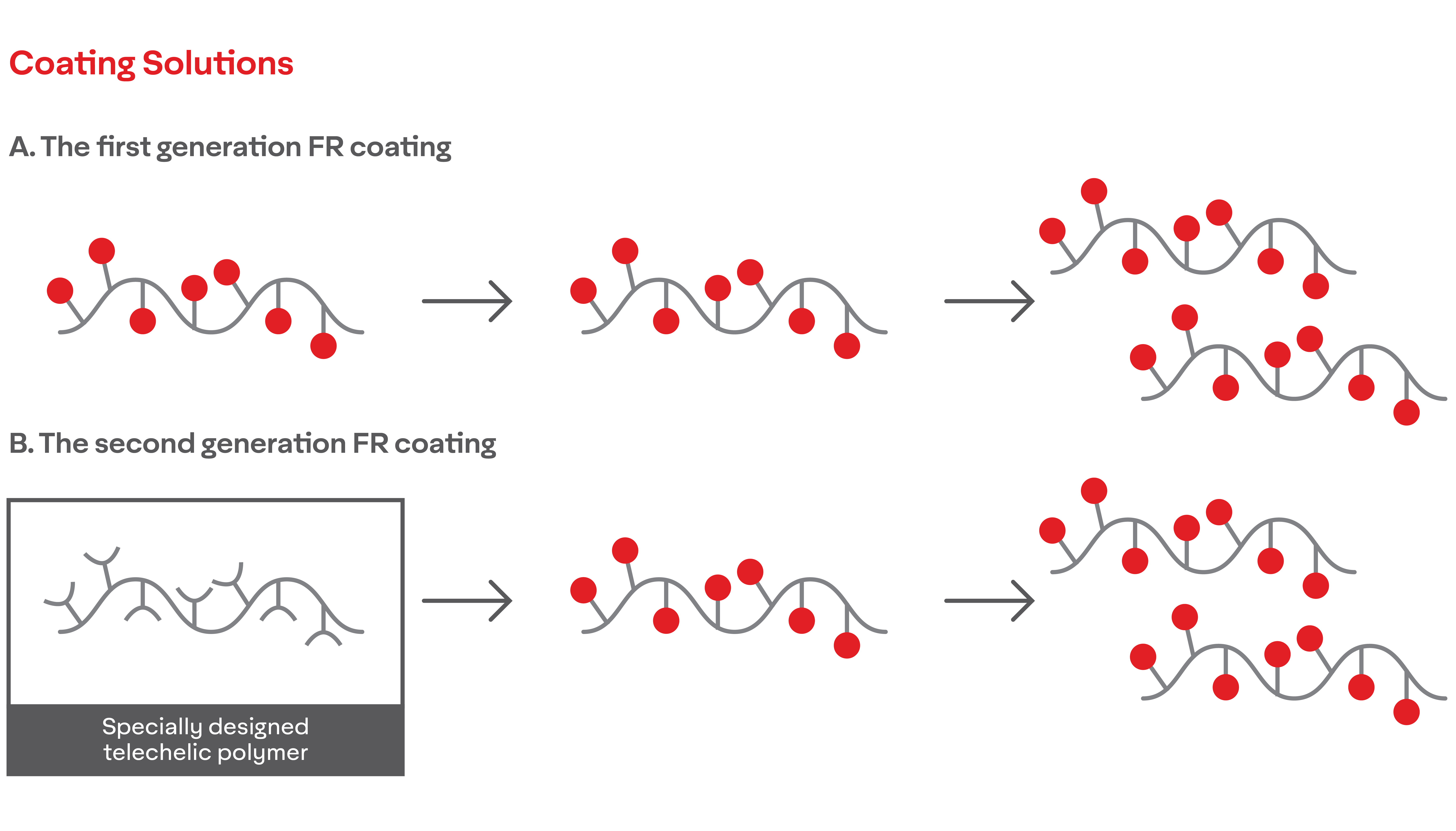
Coating Solutions
A. The first generation FR coating
- Meets UL VTM-0
- Physically missed with flame retardant
- For general portfolios
B. The second generation FR coating
- Specially designed telechelic polymer
- High transparency
- UL VTM-0
- Higher flame retardant efficiency
- No flaming drops
At the same time, Avery Dennison also commands a strong capacity for formula customization, based on customer needs. It can develop solutions for special applications such as high adhesion, high-temperature resistance, high UV or scratch resistance. The company’s flame-retardant technology platform features a relatively comprehensive product line that can meet multiple applications in industries such as electronics and automobiles
As the NEV industry undergoes a rapid learning curve, shaping our future zero-emission mobility, we are constantly innovating our adhesive and material technologies to meet the different needs of our customers. The solutions that we develop perform under extreme conditions to help to make NEV high-voltage batteries safer.
Further reading
About the author
Andrew Christie
Market Segment Manager Automotive
Andrew Christie is the Market Segment Manager responsible for the Automotive Market at Avery Dennison Performance Tapes. He has introduced many innovative solutions to the market including light weight acoustical materials and sustainable seat fabrics. His commitment to the industry continues with delivering pressure sensitive adhesives that address the challenges facing the automotive industry today.
andrew.christie@eu.averydennison.com
www.linkedin.com/in/andrew-christie